Southern Pacific
9010
Front End Work
Page 1
The
front end of the 9010
is a mess. The aborted restoration in the early 1990's at
CSRM
left it stripped of all the metal applied when the camera car
conversion took place. There are extra holes that were used
to
mount the SP plow pilot and extra slots where the MU pipes were
relocated. In addition, there is a large hunk of pilot sheet
missing next to the coupler on the right side. In order to
make
the end look good and somewhat original, all the extra holes have to be
plugged, a number of new mounting brackets and plates need to be
fabricated and the missing metal needs to be replaced.
Fortunately, the rear end is in good shape so we have patterns for all
the front end's missing pieces.
There is a long, formed plate
welded to the center of the end which is used to attach the handrail
supports and the MU step. A new one was bent using the time
honored manual approach. Brackets for the handrail supports
were
cut and new MU platform hinges were hand made. We had to
make 4 new hinges because the rear ones were
damaged. We
will also make 2 new platforms as the front one is gone and
the rear was in very poor shape. The little block in
the
forth photo is one of 4 we made that support the cut levers, 2 per
lever.
The
SP cut 2 slots in the end sheet through which the MU hose fitting
elbows protrude. I am not sure why they lowered the slots but
it
had something to do with the metal work for the camera car nose.
The slots needed to be plugged so patterns were made which
were
used to cut out pieces of 3/4" steel plate which was then welded into
the slots. The cut lever seen in the third photo is a
temporary
one which was applied in order to bring the 9010 down from Sacramento
on the U.P.
In
addition to the MU hose slots, a large chunk of the front sheet had
been removed by someone on the SP with a rather limited knowledge of
the use of a cutting torch. Does that sound critical?
Yeah,
I guess it does. But I mean it in a loving and caring way.
Another piece of plate was cut, fitted to the opening and
welded
in place. Finally, the cut lever mounting angle iron was
welded
into place. The final photo shows our blacksmith Joe Mann
test
fitting one of the new cut levers he made for the front end.
In
order to more easily get at the area above the coupler, I decided to
remove it. Much to my surprise, it turns out that it is of
the
"alignment control" type. Note the 4 ears on the shank end
and
the 4 square posts inside the pocket. The posts bear against
springs which hold the coupler centered in the pocket.
During
the camera car conversion, the SP welded a large frame on the end sheet
directly above the coupler. CSRM torched it off 20-odd years
ago
and a large amount of grinding and filler weld was required to make the
sheet reasonably flat again.
Below
is a sequence of photos illustrating the process of filling the
remaining lowered MU slot and mounting the cut lever support angle iron.
SP
also modified the front corner steps. The top step area was
blanked off and extension plates were added to the bottom of the
opening thus creating a new, lower location for the bottom
step.
The old bottom step was raised about 4 inches.
Fortunately,
the 4
remaining steps on the front end were original K-M steps and will be
used
in the reconstruction, leaving only 2 to be reproduced.
In order to take a little break from the front sheet work, I decided to
work on the missing MU platforms. Illustrated below
is a wooden mock up of the platform, made
to explore dimensions which are only available by scaling from photos.
It turns out that the model I made is about 1" too deep and
will be cut down before using this as a pattern for cutting the 1/4"
steel plate. The platform is made from a 1/4" steel top and a
2 1/2" rim, bent around and welded to the plate. On top will
be attached
aluminum 2-bar anti-skid tread plate, duplicating the existing decking.
After bending the flat around the 1/4"
plate and welding the two together, Rich cut a piece of angle iron that
was welded across the underside both to strengthen the assembly and to
provide a stop for the platform when it is hinged down into position.
The MU cable holder was formed from 1/2" bar stock and welded
in
place. Aside from sand blasting and painting, the two new
platforms are now complete.
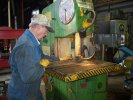 |
 |
While
continuing the cleaning and welding repairs to the front sheet, I
discovered some numbers stamped upside down into the upper left corner
of the sheet. In photo 3, the markings are turned right side
up
for your viewing pleasure. From our friends Gerold
in Austria and Richard in Germany comes the following information:
The "O" is the German Umlaut "O" with two dots/
dashes on
top) and a "V" above the
number - this is the emblem for the VOEST, Vereinigte
Österreichische
Eisen und Stahlwerke /
United Austrian Iron and Steel
Works ; they are
located in Linz, about 200 miles from Munich.
KM imported its steel from Voest at that time (and
Voest
bought its locomotives from KM). The numbers most likely
represent the manufacturing / lot number. The "F" is
probably the QA mark after checking the plate.
With the cleanup of the front end
coming along nicely, it was finally time to weld on another
newly-fabricated piece.
The gadget directly above the coupler is the MU platform
mount
and also serves as the attachment point for the front handrails and
grab irons.
Next
on the old fabrication to-do list is the front MU box.
Elsewhere
in these pages, we describe the ups and downs (actually downs and ups)
of the MU box placement. Suffice it to say there that we
decided
to put the MU box in the position as modified by the Southern Pacific.
This means that the front box will match the rear one and we
can
preserve one of the first modifications made by the S.P.
The photo on the left is the original location and on the right is the
modified location.
The
large hole is for the 27 pin MU socket
and the smaller one below it is for the 3 pin dynamic brake field loop
socket.
Next
came fabrication of the metal ducts that contain the MU wiring.
This would have been much simpler with the MU box in the
lowered
position. And finally Rich and I formed a lid and welded
everything that
can be finished together. Short of a coat of primer, the box
is
ready to be installed.
-- Update March 19, 2009 --
The
cover over the lower front end was purchased with some fabricated nose
parts and became the next project. Rich and
I spent the day measuring and cutting the pre-bent sheet of 11 gauge.
The next work day, Jon and I took care of the 10mm bolts
which
secure the plate to the frame.
-- Update April 04, 2009 --
One
of the cosmetic problems on the front end was caused during the removal
of the camera car nose. Evidently, the crew removing the nose
used
an air arc and made something of a mess of the front frame.
Photo 1 is a good example of this damage. The only way to
correct this is by building up the area with weld and grinding it down
to contour. I spent about 4 hours today doing just that and
managed to finish the edges on the fireman's side.
Once this was
out of the way, it was time to weld the MU air hose bracket in place.
As
long as the cutting torch was handy, I also opened up the step light
ports that had been welded closed.
And then,
to break up the monotony, I opened up the sand box area
on that same side. What a mess!! Not only was the
sand box
full of stuff that looked like something one would find on the floor of
a barn, but SP had done us the huge favor of completely removing the
sand box mounting flange from the face of the opening. Oh
well,
just one more thing to make from scratch. The reason for
attacking the front sand boxes is that the flanges have to be in place
before the new aluminum deck can be attached. And now to get
busy
coming up with a design.
-- Update April 24, 2009 --
Guest columnist Bob Zenk writes:
There's
a lot of grinding, welding, and filling to do to get the pilot sheet
back to the clean look it left the factory with. And there's a lot of
paint to strip! Denny Mann spent the better part of four hours just to
clean one front step well, prior to rebuilding the steps that SP
removed for the camera car. We'll move a couple from the rear to
complete the front properly, then rebuild the rear ones later.
The
new front MU box was also ready to be attached in the SP's raised
position. Howard made a temporary bracket for the back side to locate
it correctly, plus give it something to hang from, since it's one heavy
little dude. Welding the lower face of the bracket was
a challenge
because of the angle, and an example of how some easy-looking
restoration tasks aren't always that easy. When Howard was done, it was
straight as a die and restored to exactly how the SP placed it in 1964.
The First Official SP K-M Modification (so far as we know) is
re-created.
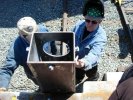 |
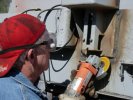 |
Very
interesting what was under all that paint thickness. Looks like K-M
used aircraft-style zinc chromate or zinc phosphate primer (green) and
then a coating of what's commonly called 'red lead' primer after that.
Then a light gray surfacing prime coat, and then the final Lark Dark
Gray. There's at least one SP-applied coat of Dark Gray after that, and
likely another coat of SP primer beneath that. It's going to take some
elbow grease and time to get all this buildup off the whole locomotive.
But for now, the front end is shaping up right along with the new nose.
-- Update June 04, 2009 --
The
brackets that support the front hand rails on the cab end were removed
during the Camera Car conversion. While not exactly part of
the
front end, they are needed to attach the new hand rails that we will be
making. I believe that the original brackets are forged and
luckily, the brackets on the rear of the cab are still there.
The
section and radius of the bracket looked to me like that of a piece of
1/2" square tubing so a piece of 5" was obtained and cut apart.
The
part with the hole is made from a piece of bar 2 1/2" by 1
1/2"
with a hole 1 5/16" drilled through. Our machinist Jeff Coker
saved me a ton of work by milling the radius on the ends of the pieces.
Their bases were ground to shape and welded to the angle
pieces.
The piece on the right is an original from the rear of the
cab
which is being used as my pattern. In the first and second
photos, the angle piece
on the left is not in the correct relationship with the hole piece as I
screwed up the pose but they were welded together correctly.
-- Update September 18,
2009 --
Our
newest crew member Dan Furtado is hard at work grinding old welds on
the front end. Dan's talents with metal are certainly welcome
on
the project. In addition, Jon Vlasak completed the piping to
the MU hose elbows on the left side.
--
Update November 07, 2009 --
Before
Dan could continue working his magic on the front end, I had to weld
the right side MU hose support plate to the front sheet. Once
I
was out of the way, Dan worked over the air arc gouges left
from years
past. He also cleaned up the openings for the step lights.
--
Update December 29, 2009 --
The
big news for this update is that we were able to move the 9010 into our
shop building so that work could continue on the front end during at
least part of the winter. Our GM Dexter Day was instrumental
in
making this happen for us.
Once
in, Jon and Gerry removed the tarps and plywood coverings so we could
start cleaning up the cab. I was able to complete the
installation of the MU box on the front end and will soon
route
the wiring up to the MU connector. Some of the brackets for
the
handrails also went on as well as one of the upper grab irons and the
MU step was test fit.
Another
big event was the removal of the rear pilot. The intent is to
repair damage to its lower surface and install it on the front.
First below is a photo from Krauss-Maffei of the SP 9003
while on
the
erection floor. The locomotive was not released from
production
like this but, it gives us a model for the rear end since duplicating
the correct pilot would not be practical and, the rear end will almost
always be coupled to another locomotive. Rich Alexander gave
a
big assist in the pilot swap and elected himself to clean out the crap
lodged inside the pilot frame. Once brought around to the
front
end, the pilot was hung in place to check bolt alignment.
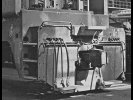
Krauss-Maffei Werkfoto
|
After
we verified that it was going to fit the front end, it was removed and
set on stands for some surgery. As you can see, the pilot has
suffered many indignities in its 45 years of life.
|